Today, the trends in construction have changed significantly, with the advancement of technology there are great alternatives for the design of buildings such as construction 4.0 and BIM methodology; and for this it is important to have a resistant material that meets expectations, with steel being the element chosen globally. This compound is the most versatile used by the construction industry, thanks to the fact that it allows the building of taller, slimmer, avant-garde structures, with better aesthetics, quick construction and 100% recyclable and reusable; which is why it is present in the big cities of the world.
According to the experts, steel expresses resistance, cleanliness and modernism, and by its nature it has the particular characteristic of offering freedom to designers and builders in projects, positioning itself as the preferred option compared to the rigidity that other materials previously used like concrete.
Within this framework, the company SEDEMI, at the forefront of construction processes, uses steel for its great creations and recommends its use thanks to all the benefits it provides, highlighting the following:
1.- Efficiency: Steel allows the design of optimal and functional structures that are prefabricated in the plant under strict quality controls, where the installation time on site is reduced and therefore there is a saving in project costs in general.
2.- Reliability: Steel structures are characterized by being very reliable thanks to the consistency and uniformity of their properties, their construction with pre-qualified and regulated procedures under international standards that guarantee the quality of the work.
3.- Light weight: Steel is a much lighter material than concrete and highly resistant, resulting in light infrastructures, allowing the construction of tall buildings, with large spans and better use of space.
4.- Sustainability: The environmental impact of steel is less than any other material since it is 100% recyclable and degradable, making it possible to reuse or relocate it once any structure is dismantled. After being recycled, it does not lose its resistance and physical properties, which is why buildings can be certified as eco-efficient or sustainable.
5.- Used in BIM methodology: Virtual models created under BIM technology allow the planning of projects in more detail, improving decision-making and avoiding inefficiencies. Once the metallic structure model has been integrated and validated in BIM, through an engineering process, the manufacturing plans and files with defined industrial standards are generated.
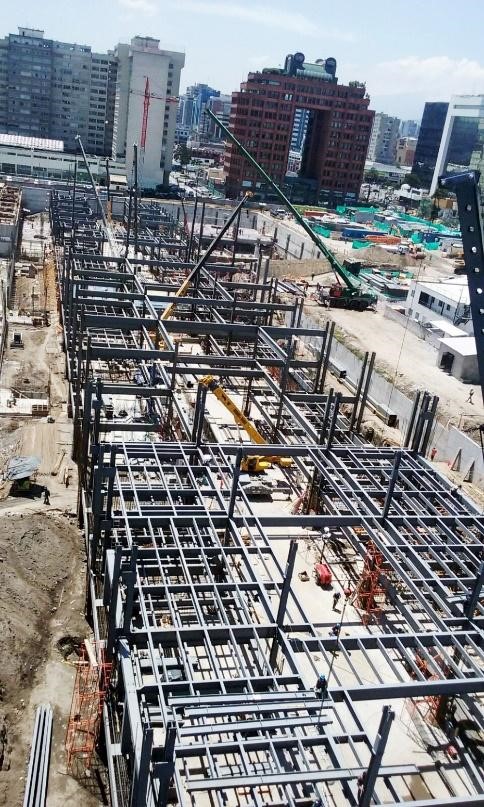
6.- Resistance: Steel is very resistant, ideal for projects in the urban, industrial, energy, telecommunications and oil sectors. It is also perfect for working in areas of high seismic risk.
“In conclusion, steel construction has shown to have a highly satisfactory behavior in the face of natural phenomena due to the ductility that characterizes the material and it is profitable for large constructions, which is why it is the favorite for all types of structures. At SEDEMI we work with this element under the necessary rigorous quality standards and a team of expert professionals in order to provide efficient and qualified work,” commented Esteban Proaño, executive president of Grupo Corporativo SEDEMI.
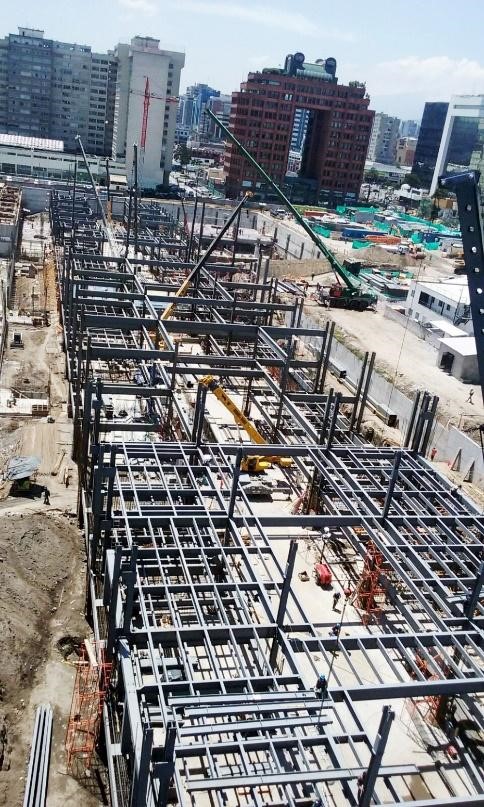
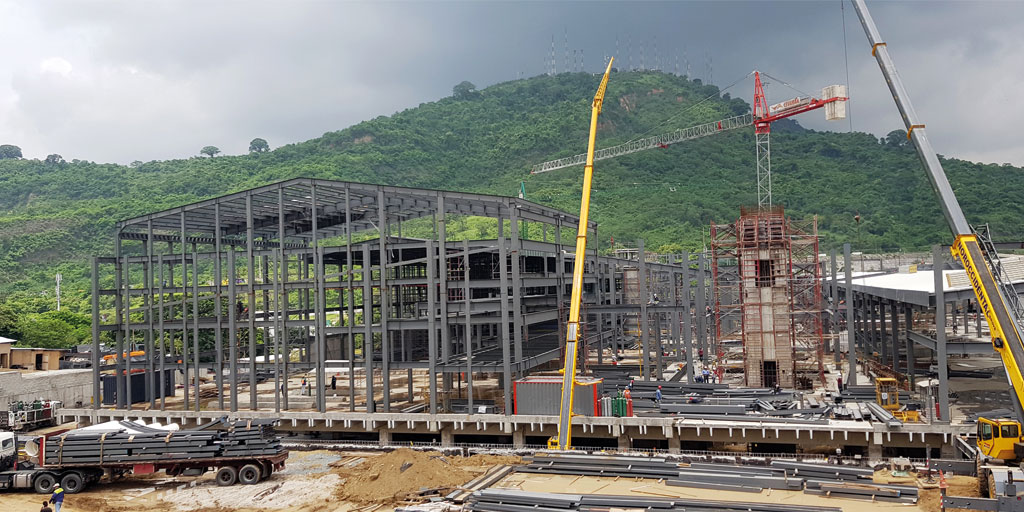
